PROJECTION
21 Jul 2025
LETTING LIFE HAPPEN
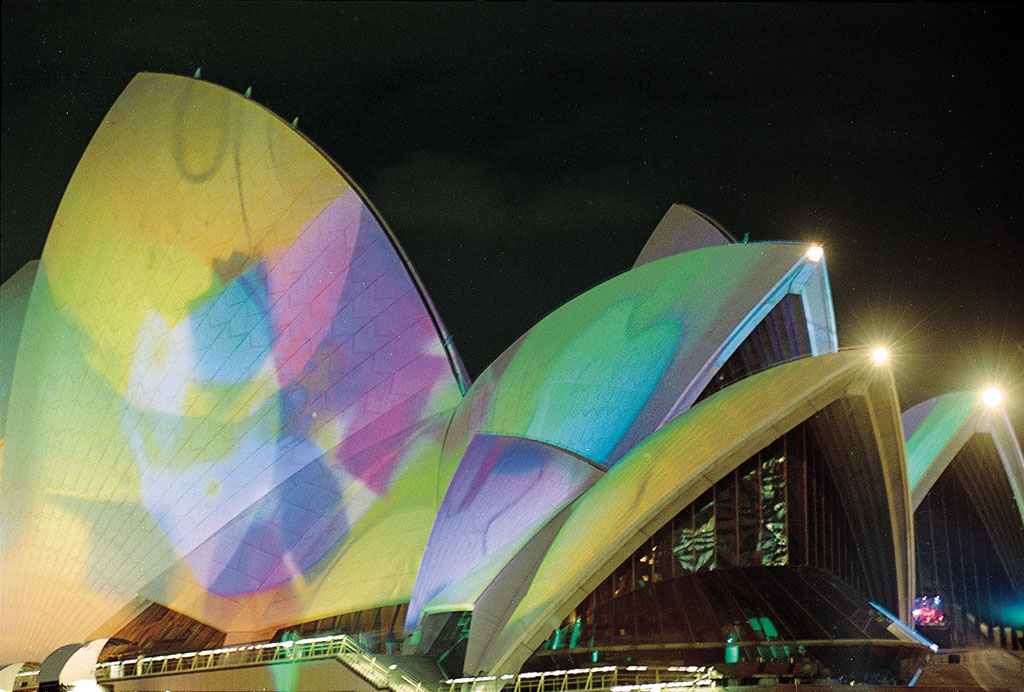
Subscribe to CX E-News
How Gobo Production Came To Australia
As my daughter takes over the reigns of the day to day running of our company, Gobotech, I reflect on the last 30 years and how we became the hub of gobo manufacturing in Australasia.
Growing up in Sydney in the 1980s, I would ride my motorbike down Parramatta Road coming home from my electronic engineering class. I think it was the flashing light display in the Lightmoves windows on Parramatta Road that inspired me to get into lighting. That and putting a red and blue Par38 onto the chrome of the church drum kit! Still not much that beats that combination.
After a few years in electronics I quit my cushy job to go on a backpacking adventure through Europe, something I wish everyone could experience. As luck would have it, on my travels I also met a young Swedish lady who would eventually become my wife. With a work permit organised I got a job in Stockholm working for an AV company, initially repairing equipment and later lighting events, from rock ‘n’ roll shows to corporate and trade shows.
This was the early 1990s, and I was having a ball working with some awesome and creative people, as well as the odd international or emerging superstar.
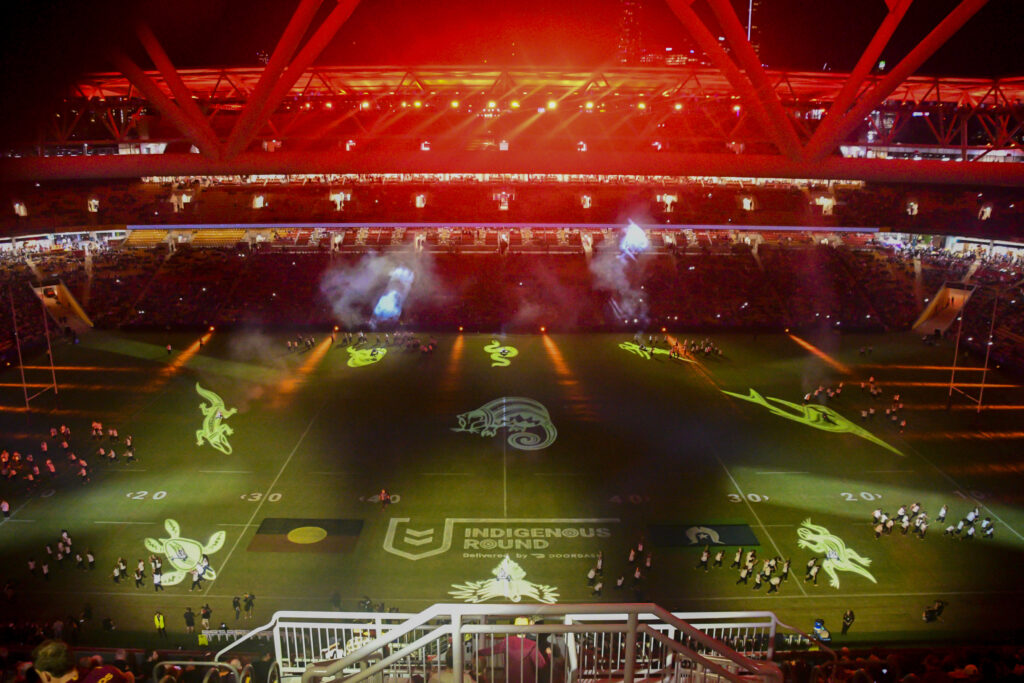
I also sold Italian disco equipment and repaired lots of gear. It was in the back of that service room that I first dabbled in gobo making. A gobo is simply a disk that you remove material from to let light through in some parts and leave shadow in other parts. Initially, I cut holes in thin aluminium but eventually I got hold of mirror glass disks from Beacon coated with a photosensitive resist. Beacon in Sweden had a simple gobo making kit with UV fluros, allowing me to expose and etch the glass disk in acid leaving an image cut in the mirror substrate. It was far more sophisticated than a cut-up Coke can with nail holes for a starry sky, and pretty cool I thought!
Some of my very first glass gobos were for the Nobel dinner in Stockholm. I’d reduce designs on the office photocopy machine, print them, and then expose them through paper for what felt like an eternity using the Beacon UV lightbox. Finally, I’d develop and etch the image in acid. The results were crude, but absolutely usable.
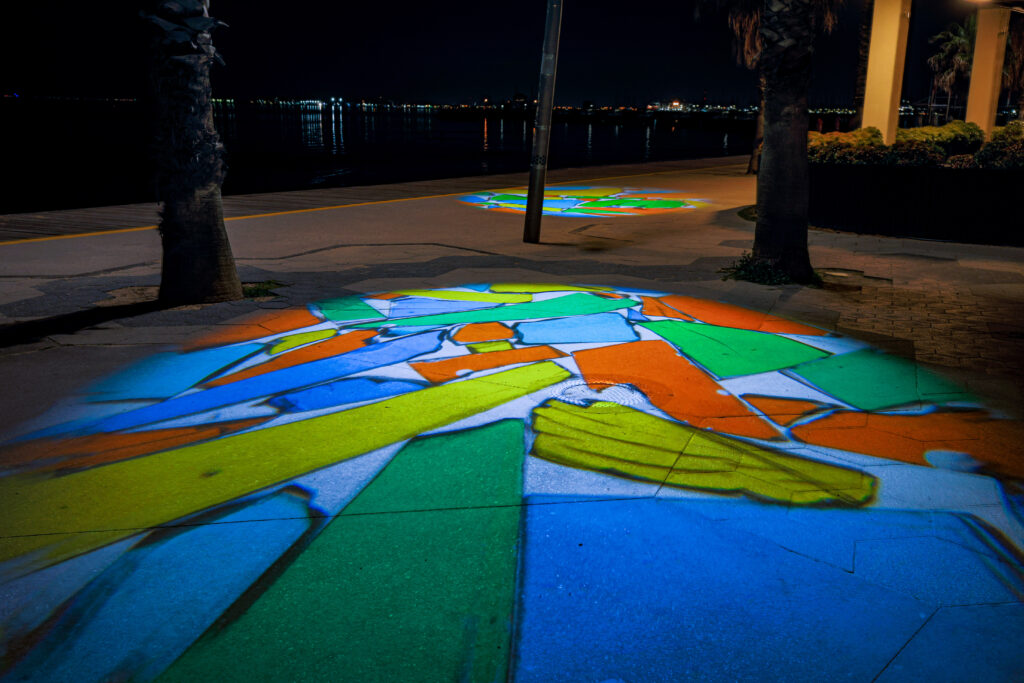
By 1996, I was married with three kids, the youngest four months old, but I was ready to move back home to Australia. A chance meeting with Micke from Beacon was, unbeknownst to me, about to set my new course in life. He asked if I’d be interested in bringing their new, patented colour gobo process to Australia. Sure, I said, I can give that a go.
Colour gobos in the mid 90s were horrendously expensive and very few people had the know-how to make them. Micke’s process, however, allowed us to stock super-thin (0.1mm) standard dichroic glass and produce custom gobos at a fraction of the cost. The CMYK colour mixing process involved laminating the thin colour layers to the thicker black layer and still maintaining the focus on all layers. Still not cheap, but feasible to make and sell.
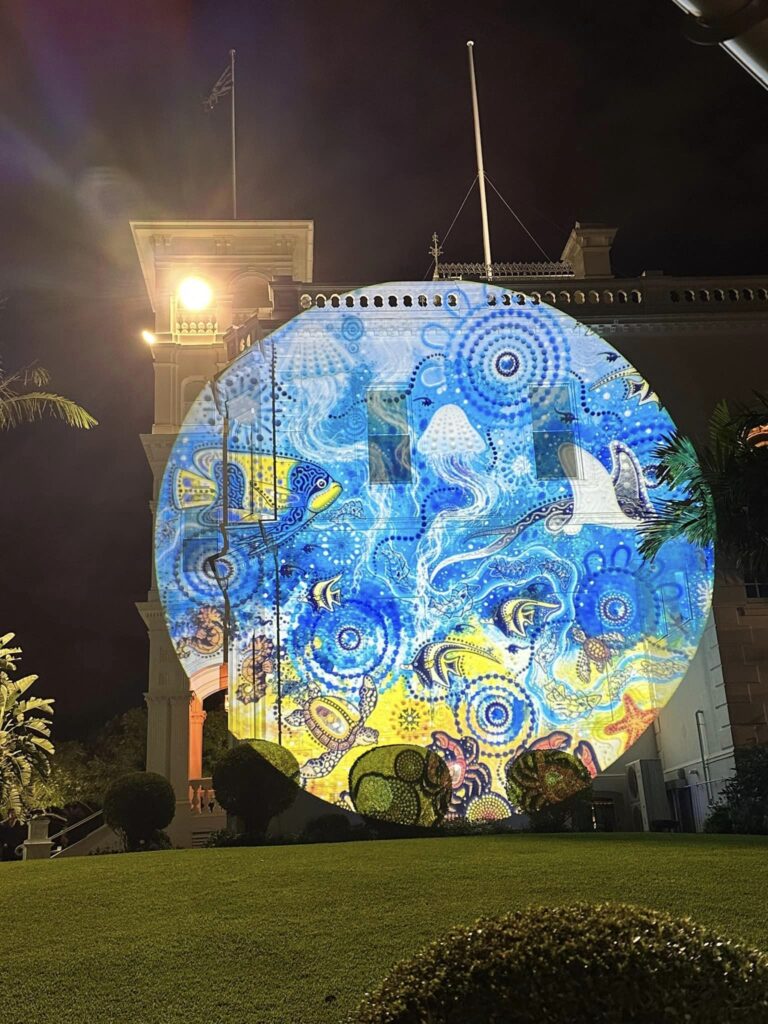
I had no grand plan beyond warmer weather, but Joe Labero, an illusionist in Stockholm, was embarking on a few years of shows at Jupiter’s Casino, so we packed some stuff in their shipping container to save a few dollars. We had also saved some Gold Coast Aussies in a campervan from death by hyperthermia in a blizzard, so it cemented our decision for the Gold Coast as our destination. They had a house organised for us as we arrived and our new stage in life was about to begin.
I installed an old AGFA Repromaster in the garage and built a darkroom. The Repromaster would allow me to reduce the size of a printed image and process a film that I could use for exposing gobos. We still produce film today but not with the old Repromaster.
I needed a real job, though, so offering to repair gear again I was quickly snapped up by Entertainment Lighting and Sound, at the same time making gobos at home in my garage.
I had a great time working with ELS, once again some awesome people, but my sideline, (Lighting By Design), steadily grew. After doing the ENTECH tradeshow around 1998, I got so busy I had to quit and concentrate on the gobo making, still out of home, but it was now a full-time job.
When the New Years Eve 2000 and Olympics festivities were being planned, I got contacted for projections onto the Opera House. It was a lot of images, and a default on payment would have sunk me, but I got the deposit in time to get the job underway and get the job done. A few weeks out from NYE and I was contacted again to make a type of oil wheel effect to shoot onto the Opera House. The light chosen was a 4,000 Watt Coemar NAT. An oil wheel normally has a wheel rotating through the beam so that it has plenty of time to cool, a bit like passing your finger through the flame of a candle. The NAT, however, had a gobo wheel with the image constantly in the 4,000W beam. They had already approached other manufacturers to do something, but nobody was crazy enough to attempt that. I said I’d give it a go, but no guarantees!
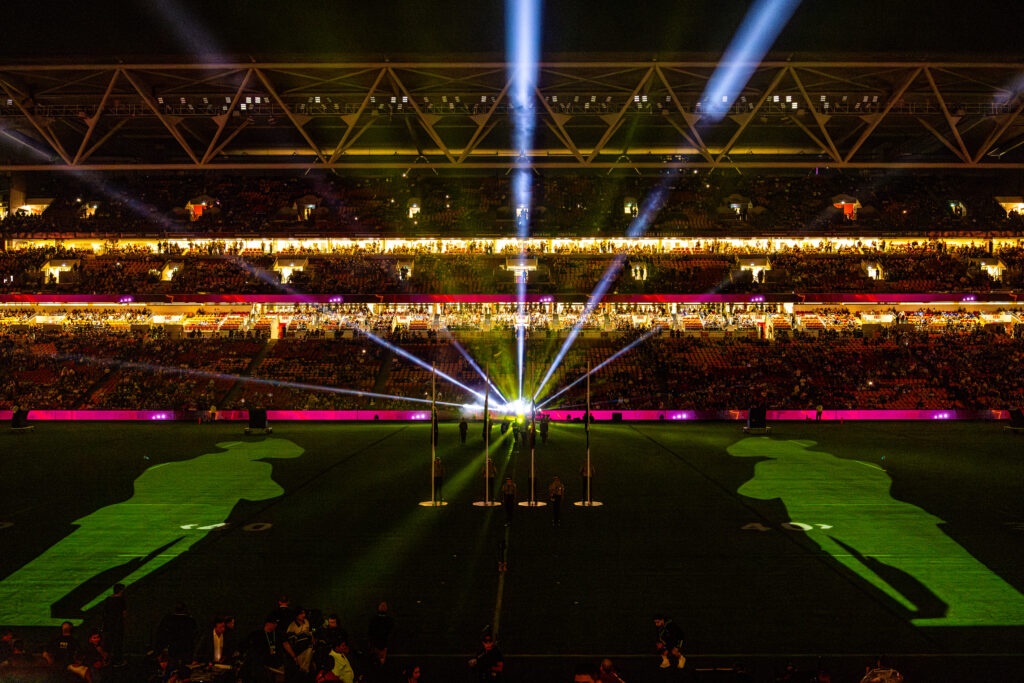
They sent me up a NAT for testing that I had to get wired direct into my switchboard and I lit up the sky like the bat signal. Christmas 1999 had the whole family sitting around a table gluing layers of clear glass and dichroic glass shards together and filling the gobos with synthetic oil through a syringe. I flew down to Sydney with an attaché case full of about 200 full colour gobos and the new oil filled gobos. I wasn’t going to trust anyone else with that delivery!
The job was a success and all the gobos were used nightly for a month. I believe we supplied 40 of the oil filled images, and only one had failed by the end of the month. But I’ll never do that again!
By now, I was making plenty of glass gobos but I did not have the equipment or skills to make steel gobos. I used The Gobo Factory for steel gobos and they would use us for the glass. By 2002 it made more sense for us to join forces so Lighting By Design merged with The Gobo Factory to create Gobotech Pty Ltd and moved into a larger factory. Now we could offer a complete range of gobo solutions from a single company.
The rise of LED lights brought a new challenge, and we initially thought glass gobos might be replaced by DIY plastic film.
We supplied some high resolution film for a while, but in reality, most LEDs quickly became so powerful and gate temperatures so hot that today, most moving lights are too intense even for steel gobos, demanding the ultra-high reflectance coatings and high-temperature glass that we use today.
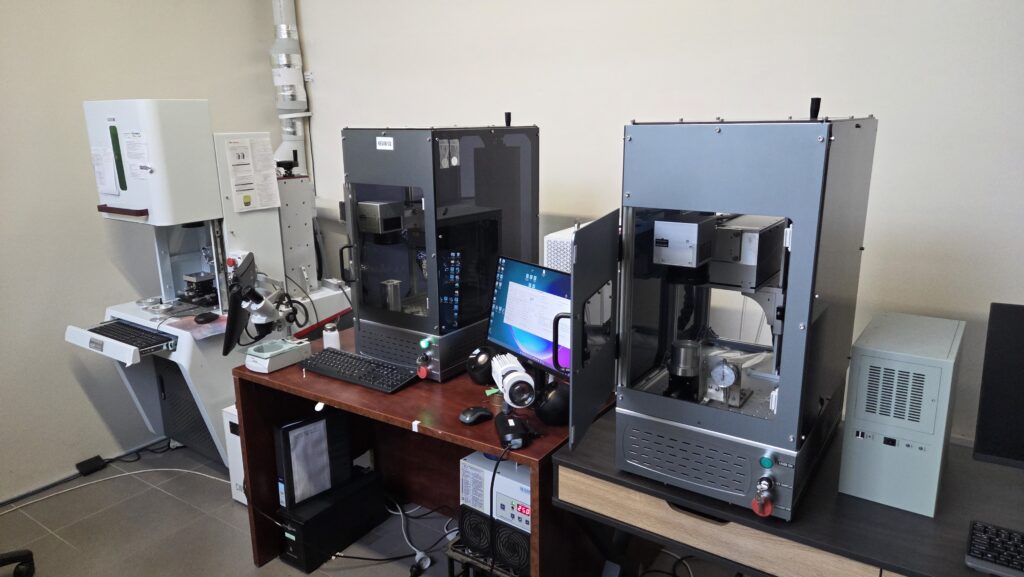
The processing technology from 1996 to today, 29 years later, has certainly changed. Today our factory is equipped with multiple, ultra-high resolution, laser marking machines suitable for the new coatings. We still choose acid etching for some glass production as the colours tend to be more vibrant but many designs, especially the small, detailed gobos are now best manufactured with the new lasers. Steel production continues with a new large conveyorised spray etching machine, though these days its only used about once per week as steel is simply unsuitable in so many of the new lights.
Over the years we had found that when bars, restaurants, and hotels wanted to promote themselves they were after permanently mounted projectors. The event industry and rental companies did not have the right equipment for this, and the customers ended up with poor choices, making the projections look terrible at times. To fix this, I spent years researching products and making personal visits to manufacturers, finally building up the connections and trust with companies that would supply to our specifications. Today, we have a boutique range of simple but functional lights that we individually finish off, test and adjust for each individual clients needs, all done in our Gold Coast factory. These lights are sold under the Grand Lighting brand and can be found throughout Australia and New Zealand, lighting up council parks and walkways as well as hotels, bars, and restaurants. The new Industrial range and Line Projectors replace painted lines, pedestrian crossings and warning signage in large factories and warehouses throughout our region.
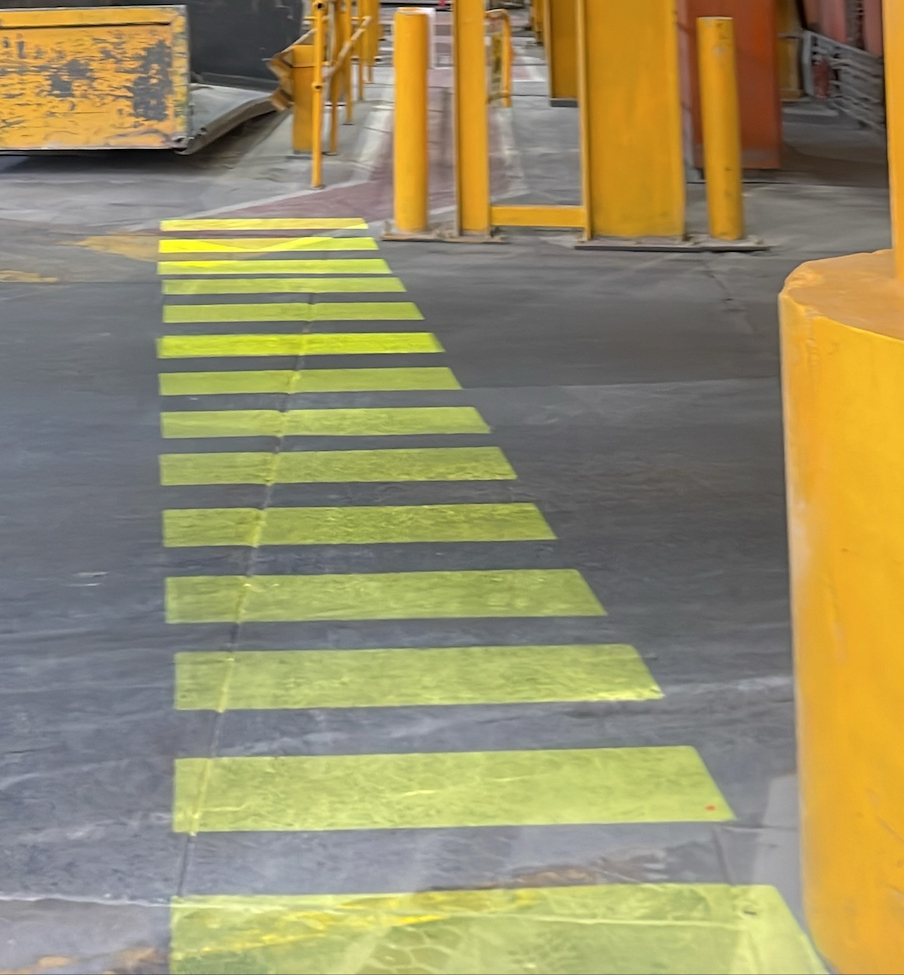
to project a bright pedestrian crossing that changes to stop signs for pedestrians as forklifts approach.
Life has been quite a journey so far and I’ve had the pleasure of working with many wonderful professionals both in Australia and internationally. After nearly 30 years of making gobos, it’s time for the next generation to take the reins. My daughter, Sara, was two years old when I started this venture in my Gold Coast garage and, like her siblings she had no intention in following in her fathers’ footsteps – she became a nurse instead. Eventually, she saw the light (pun intended), and decided that making gobos was a lot more fun.
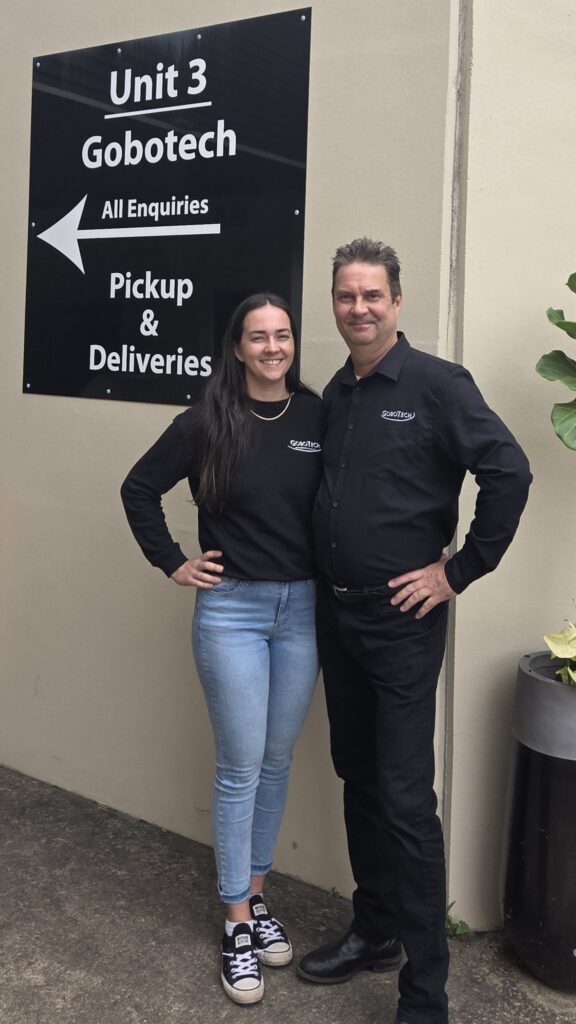
13 years later, she’s a highly skilled and dedicated young woman who now, I have to admit, is even better than me at this and will continue with her staff to provide the service that got us here.
I’ll still be around in a support role, and I’m confident our small family-run company with four staff will be around to service Australasia for many more years to come. Sara is having fun refining designs and spearheading new sales for our Grand Lighting display projectors, as well as the cool new Line Projectors for industry. Peace everyone and thanks for the ride so far, I’ve had a blast!
About Gobotech
Gobotech Pty Ltd, based on the Gold Coast in Queensland, is one of only a handful of full-service custom gobo manufacturers in the world.
Gobos are disks that get fitted into lights to project images and logos. There are stock standard images as seen in every moving light out there, but you can also get custom images manufactured.
Gobos are seen every day on TV and in the movies but we constantly get asked “What is a Gobo?”. People don’t realise they see them almost daily. We have supplied many movies over the years, including Waterworld, Batman and Star Wars, but it can be easy to miss when you watch a movie. You may not realise that the light coming through an overhead grate as Luke fights Darth Vader in a tunnel with a lightsabre is simply a steel gobo in a profile shining from above.
That’s the magic of the movies.
Gobotech manufacture full colour, black and white and steel gobos in our factory, as well as supplying a range of display projectors and factory signage solutions including the new Line Projectors.
Hundreds of standard images as well as full information on our projector range is available on our website:
Subscribe
Published monthly since 1991, our famous AV industry magazine is free for download or pay for print. Subscribers also receive CX News, our free weekly email with the latest industry news and jobs.