News
12 Aug 2016
Meyer Sound: Everything Matters
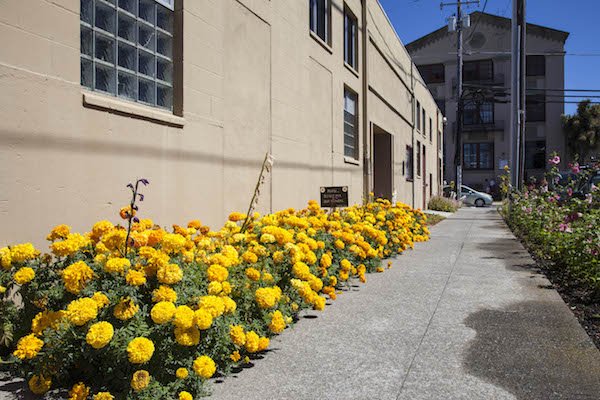
Subscribe to CX E-News
FACTORY TOUR; by Julius Grafton
Since inception in the 1970’s Meyer Sound has occupied space in San Francisco’s Berkeley precinct and today 350 people make almost everything they sell, right there. It’s an eclectic precinct – the organic food market at the end of the street can feature a Sitar player. A gourmet hotdog tent does lunches up on the corner.
But beyond the neat pavement flower beds of sun flowers and petunias lie a set of facilities tailored to the science of audio. Because founder John Meyer is an astronomy enthusiast, each facility or building has a planetary name. Naturally I start my tour at ‘Earth’.
John McMahon, Vice President of Solutions and Strategy greets me, and we move into the area where speaker cones are made. Meyer has made their own transducers for over twenty years, which jives with their obsession for accuracy.
We visit the cone manufacturing area where a 5,000 litre tank contains water laced with an unspecified but not toxic chemical compound. Into this a hopper dispenses a measured dose of fibres. If they are making a 12” cone, they insert what looks like a stainless steel pasta strainer into a vacuum head that lowers into the solution and sucks onboard a prescribed layer of fibre.
This fragile mushy porous cone is then placed on a heated mould, applying pressure until it is baked hard, then it is coated. It is weighed, and measured and if perfect sent down the line for bonding with the surround.
All up the Meyer plant makes one speaker every 30 seconds. They often work multiple shifts to keep up with demand, as product such as Cal come with up to 96 tiny drivers (speakers).
It is laborious, “there’s a lot of touch time”, says John, as “it yields consistency. John Meyer says it is easy to build one great loudspeaker but it is not easy to build thousands.”
This is a detail rich tour, walking through the complex, visiting Venus, Saturn, Mars and other out-stations up and down the road. Meyer Sound has a ‘dynamic’ manufacturing system where smaller orders of just several products can be made, because there is no warehouse full of finished product.
Instead they use the Kanban system where sub sections and vendor parts, that is the things Meyer don’t make, are all lined up ready to build. John explained that vendor components include steel and timber, as there are many suppliers for these nearby and Meyer can’t add value to the process.
“It’s in the vendor’s interest to keep the stock lined up, so we can buy it and use it,” he said.
This amazing dexterity means literally thousands of parts of the product range are all lined up, usually sub-assembled, waiting for an order. When sequenced, an assembler starts the process and works right the way through to signoff. This means each assembler has a range of products they might build, which gives them ownership and invests them in the process.
I saw it in action – a guy is building a LEO. He starts with the empty wood cabinet, on a trolley, and visits the bays for each part required. A job packet of serial numbered test sheets is collected on the way. Each component has already been tested. At the end of the line, he signs it off to Quality Control, where the system is put through a set of tests.
Along the way every component comes with a test report, so at the end of assembly there is quite a packet of paperwork which is then all scanned and digitally attached to the serial number.
Prior this the electronics module (containing amplifier and processing, as every Meyer product is self amplified) has been to hell and back – courtesy of a test rig that bakes and freezes (zero to 50 degrees C) which I am told trends to identify any loose or out of tolerance items.
Quality Control answer to Helen Meyer, who has a major role in compliance and oversight and of course is a co-founder. The message I see is that test and monitoring of performance of components and systems is a major investment at Meyer. Manufacturing in this era usually relies on sample testing of batches, but at Meyer they test every component, then they test every manufactured item.
Over at the final test zone, all systems are run up in one of several test chambers, where they need to meet tight (and secret) company tolerances otherwise they are not shipped. Because the components and sub assemblies have already been tested, it is rare for a final product to fail.
If any variation at all exists it can be compared, as they keep a ‘master’ of each product in hand for comparison testing. This way, one master of everything is there for real time comparison tests, just in case. This eliminates specification fade.
In the electronics factory, every finished amplifier or processors (such as Galileo) are run through the hot and cold oven, ranging from zero to 50 degrees Celsius, whilst running. John says this is the only way to truly test fit, fixing, wiring and components.
We walk through research and development, and John jokes that he will use the ‘Men in Black’ pen on me after. It must have worked because I didn’t see anything, despite the department being large.
The tour winds through a listening room, beautifully furnished with paintings of the cosmos. It has some nasty concrete walls, including a hob several metres down from the ceiling.
In here is a Cal 96, a steerable column array and this room is perfect to demonstrate what it does. In normal mode, it acts like a column array and disperses audio straight ahead in a 120 x 30 degree pattern. The room sounds nasty, since a lot of that audio is coming right back off the concrete hob and the back wall. Flipping a switch to steer the audio down to the listener radically improves the acoustic. The difference is startling.
John points out that Cal is accurate up to 10kHz, which is a lot of steering, and thus sounds ‘more musical’. I can only agree.
At the conclusion of the tour, the beautiful Pearson Theatre contains a Constellation System which is renowned worldwide for its unique processing that can change the audio characteristics of a space.
The theatre was designed very dead, so that a person talking from the podium is a little hard to hear. Switching the Constellation System which in this theatre utilises 20 microphones and 47 small speakers (each processed individually) and suddenly we have an 0.4 second room – more reverberant – and the spoken intelligibility snaps into place.
John demonstrates various settings, adding ‘liveness’ to the room until it is a mega large reverberant hall like an old church.
We have a discussion about SPL and the wild claims some manufacturers are making these days. “We measure broadband over two hours, not some silly peak measurement. Imagine you had a light globe, and you measured how bright it got just before it fails.”
Thus the uniqueness of Meyer is laid out – they have the CAL to direct and steer the sound to where the people are. They have the Constellation System to ‘fix’ and enhance a venue, allowing multiple types of performance at the flip of a setting. Someone called it ‘electric plaster’. And of course the LEO Family of loudspeakers providing unique solutions for touring and fixed installations.
Last of all, they have a free spirited culture, seeking to ‘do the right thing’. It is very clear that the firm reinvests heavily in process and design, and that if they ever ship anything faulty a big investigation will find the source of the problem.
Subscribe
Published monthly since 1991, our famous AV industry magazine is free for download or pay for print. Subscribers also receive CX News, our free weekly email with the latest industry news and jobs.