News
21 Apr 2022
Novastar’s new XR Production workflow
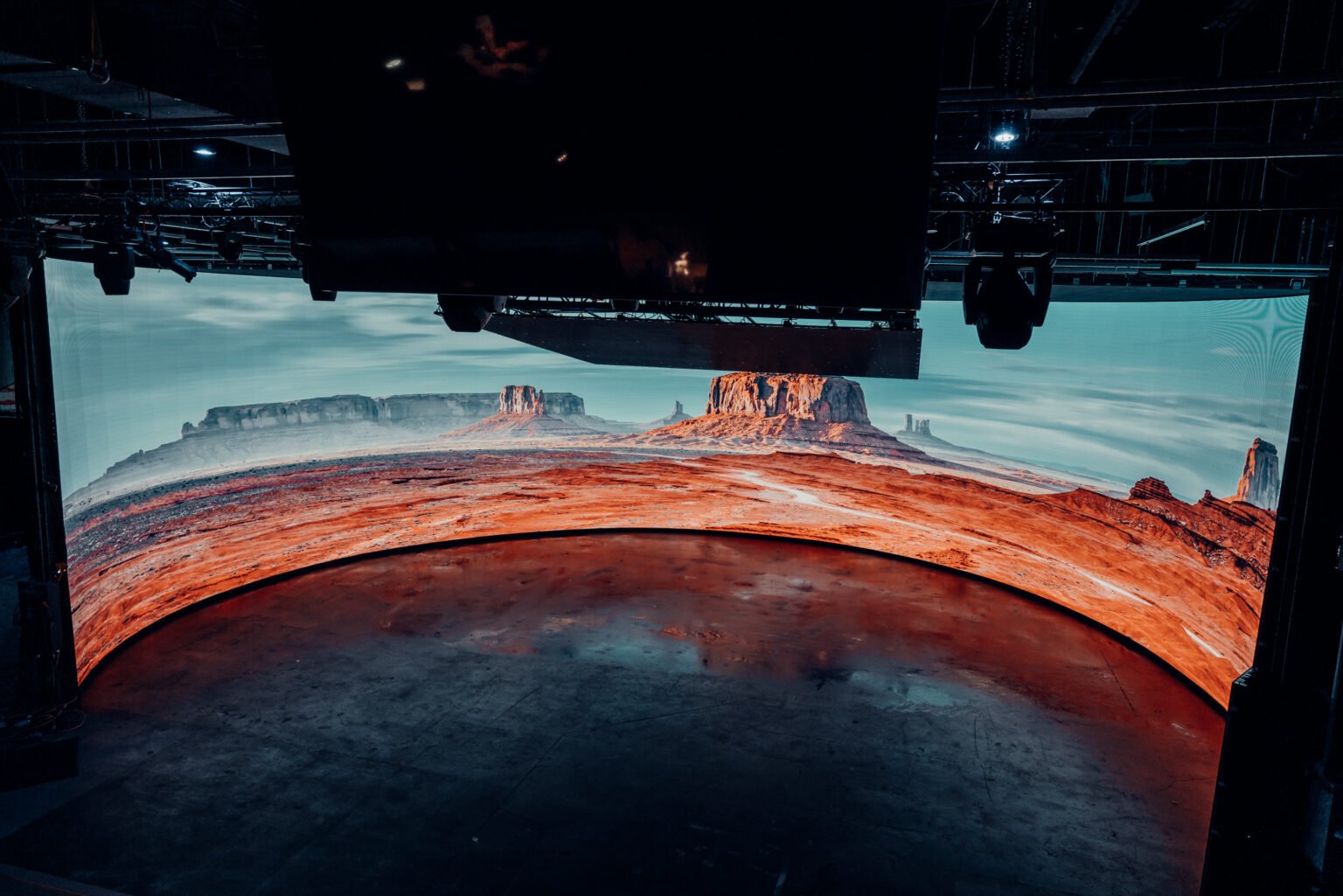
Subscribe to CX E-News
xR virtual production is becoming increasingly popular. LED screens with their realistic colors and higher dynamic range can better provide an immersive shot environment for actors compared to traditional green screens, and can also eliminate a lot of post-production. In recent years, it has been more and more widely used in the fields of virtual staging, advertising production, film, and television.
In order to improve the efficiency of the xR studio set-up, make the work of screen allocation and adjustment easier, and at the same time effectively solve display problems during the shooting process, Novastar has launched a new control system solution for xR virtual production. The system is comprsied of the MX40 Pro processor, visual management software VMP, and A10s Pro receiving cards.
The first step is to build and configure the LED screen. In a professional xR virtual scene, the LED screen is used as the main background for the virtual production. Usually, the LED screen is very large and curved, sometimes it is also an immersive studio made up of wall, ceiling, and floor screens that are stitched together. In most situations, the xR virtual scene requires multiple control devices to be cascaded and spliced together to light these screens.
In order to make the control and management of all devices easier and more convenient, Novastar have introduced the design concept of group management in the program, which allows all control devices to be managed in groups with displays, and then the parameters of all devices can be adjusted all together based on different groups.
The new solution uses a high-bandwidth gigabit network interface and supports TCP/IP protocols for hardware and software communication, resulting in a significant increase in data transfer rates, which allows for timely feedback on all operations on the screen. You can see the status of the cabinet connection in real-time and adjust the connection if you find any problems during configuration, making the whole process very easy and efficient.
In addition, due to the physical characteristics of positive and negative tolerances when putting cabinets together, bright and dark lines can appear between cabinets or modules. In the VMP software, it is very easy to eliminate the bright and dark lines. If you want to eliminate it, you just need to select the area to be adjusted in the software interface or position the cursor directly on the screen where the bright and dark lines are, then face the screen and slide the mouse wheel or click the keyboard up and down keys to quickly adjust and eliminate the bright and dark lines.
Once the configuration of the LED screen is finished, we often need to make quick adjustments to the display by aligning it with the camera system for color calibration or stylised toning, depending on the needs of the site director or visual effects designer. The new solution offers a wide range of colour adjustment tools to make it easier to meet a variety of color mixing needs.
On the output side, the colour picker tool enables the replacement of any colour on the screen. The system supports 14-channel colour adjustment, so that when the user finds that the picture has a colour cast, hue, saturation, and lightness can be adjusted to make it display more accurately.
For more professional toning needs, the solution also supports curve toning and 3D LUT files. Anchor points are added to the color curve for the red, green, and blue channels which are adjusted independently. Local 3D LUT files can also be loaded with a single click, and the image on the screen is transformed into various styles of shading as if changing filters.
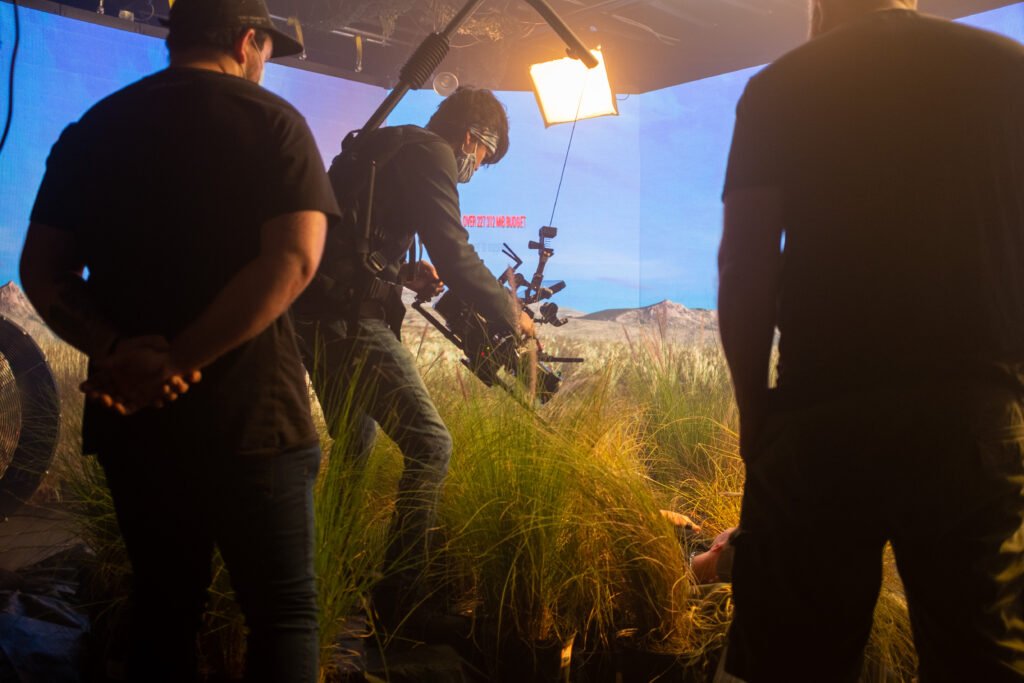
On the input side, the black level and contrast can be adjusted independently for the highlights and shadows of the input source screen, resulting in a more comfortable contrast between bright and dark and an optimal rendering of details.
In addition, the display parameters can be set in advance for different scenes and can be switched flexibly at the touch of a button when shooting.
When shooting on site, the LED screen is a scanning screen and the camera captures the image at a fixed shutter speed for exposure. When shooting together, if the timing and frequency of the screen scanning do not match the timing and frequency of the camera shutter opening, problems such as scan lines and black lines will occur. For virtual productions, above problems can lead directly to the film becoming invalid.
With shutter fit, phase offset technology, and external Genlock signal, the screen is precisely synchronised with the camera and adapts to the camera’s shooting parameters, thus solving problems such as black lines, scan lines, and picture tearing during shooting.
In addition, the MX40 Pro supports Frame Multiplexing, inserting different content footage, which are for different capturing angles, into a single video source, allowing multiple cameras to output footage from multiple perspectives simultaneously in just one take. It can also insert pure green background footage for easy post-production and adjustment, thus significantly improving shooting efficiency and reducing shooting costs.
The Novastar xR virtual production Control System solution is a comprehensive solution from screen configuration and display adjustment to the processing of shooting defects, bringing a more convenient and efficient control experience for xR virtual productions, while ensuring perfect display quality.
Subscribe
Published monthly since 1991, our famous AV industry magazine is free for download or pay for print. Subscribers also receive CX News, our free weekly email with the latest industry news and jobs.