News
9 Sep 2021
TSA’s Adelaide Scenery Workshop
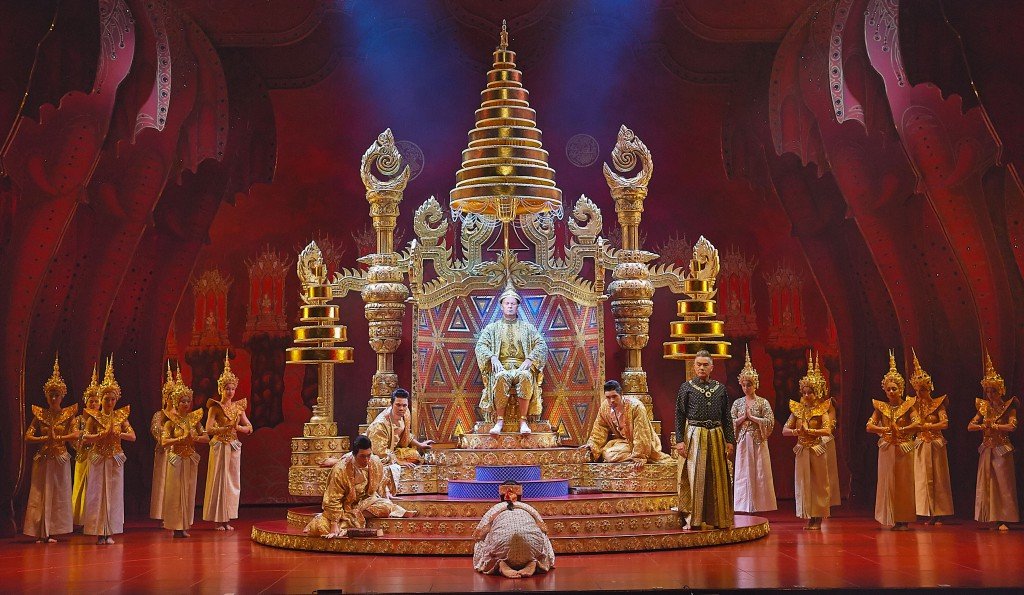
Subscribe to CX E-News
The tradition continues in SA
(Lead Pic: The King and I -photo by Brian Geach)
I must confess, as a South Australian who spent a decade working in professional theatre, I had no idea that 65% of all commercial theatre sets in Australia were manufactured in Adelaide at a workshop with an international reputation for quality.
Back in 1979, with a production of Evita to build, the Adelaide Festival Centre Trust created a workshop for scenery engineering and automation. For years, they worked across two sites, divided into mechanical and carpentry, working on set builds like the automation masterpiece Phantom of the Opera, and iconic shows including Cats, Matilda, Billy Elliot, Wicked, Les Miserables, and Moulin Rogue!
Amalgamated into one site six years ago, the workshop continued to produce high-quality set pieces until 2021, when ageing equipment, staff retirements, and COVID, meant the Adelaide Festival Centre Trust were struggling to keep the doors open. In a serendipitous moment, while on-site for a completely different reason, Theatre Safe Australia’s Director Stuart Johnston found out about the workshop’s existential crisis and decided to step in.
An Australian success story themselves, Theatre Safe Australia began life seven years ago when Stuart, a staging and technical manager who’d led venues and toured with shows like Cats, saw a gap in the market for theatre technical services. The company started out doing mechanical servicing and safety inspections, and it wasn’t long before their customers started asking for equipment sales and installation. The business expanded into performer flying, automation, and rigging services, and have now worked on shows including The Lion King, Moulin Rouge!, and Hamilton. Their upcoming projects include an automation system in Korea for Hadestown, Opera Australia’s The Ring Cycle in Brisbane, and new Broadway smash Jagged Little Pill. Headquartered in the Gold Coast, they also have an office in Sydney, and now in Adelaide.
Book of Mormon Wicked Matilda
“The Adelaide Festival Centre Trust were looking at streamlining their resources, and making adjustments to their operating structure,” relates Stuart. “We already had a good relationship with the AFCT, and I got into a conversation with the board, mainly about how to retain the workshop and keep the jobs in South Australia. We’ve come to an arrangement where the workshop remains basically the same, operating out of the same premises, with most of the same people staying on and bringing the workshop’s core values with them.”
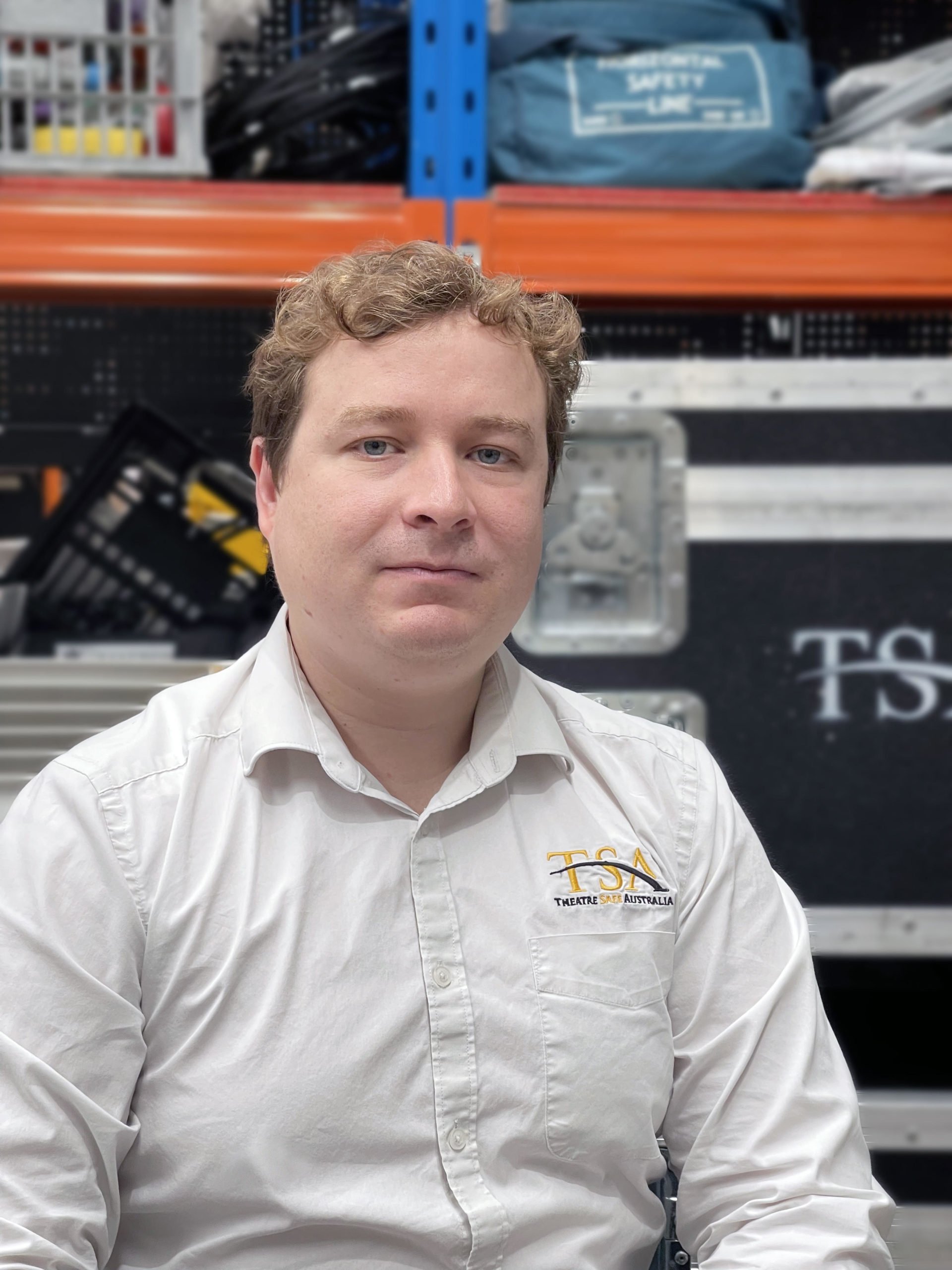
Those core values include attention to detail, dedication to build quality, and a passion for educating the next generation of technicians. “The inherited skill and knowledge of the workshop’s staff is its greatest asset,” praises Stuart. “They’ve been producing the highest quality sets in the industry for decades. The knowledge has stayed in-house, as the staff have been really well looked after and stayed with the workshop. The core staff love to train the up-and-comers and will reach out to TAFE and the Universities to get people in to develop. Some of these skills are both irreplaceable and disappearing. Being able to construct and mould scenery by hand is a dying art, and we need to keep it alive.”
“This new relationship opens up opportunities for TSA and the workshop,” continues Stuart. “Having the staff and their knowledge as part of our organisation is a huge thing for us. Along with our automation, rigging, and flying services for shows, we can offer a complete theatrical end-to-end solution to producers. Open communication with one company will save headaches for producers and designers, and we won’t be trying to integrate automation and other elements into sets someone else has built. Everything will be addressed at the design stage.”
The Old Guard – Mike Price – Scenery Workshop Manager
Current Scenery Workshop Manager Mike Price has been with the workshop almost since the beginning. A machinist by trade, Mike started out at The Adelaide Festival Centre as a plant operator, technically part of the maintenance department. When the AFCT started to build scenery, Mike and the mechanical services crew would hire a space, take their gear out to it, build the show, and bring it back to the theatre. After a few rounds of this, they were established at a permanent facility in Gepps Cross.
“We were split into mechanical and carpentry, and I started in drawing and design,” says Mike. “In mechanical, we’d concentrate on structural steel and hydraulics. We developed our own stage automation system, Stage Master, which was co-developed with another company. Phantom of the Opera was the first really big show with a lot of automation for us. In addition to designing and drawing, we’d physically build the sets ourselves. We’d then do the bump-in, get the show up and running for rehearsals, go home, them come back for the bump-out, and get it packed up ready for next venue. We’ve toured shows in Australia, South Africa, New Zealand, Singapore, Taiwan, China, and Korea.”
After 35 years with the same employer, which is not unusual at the workshop, I asked Mike why he and others have stayed on so long. “It’s unique and interesting work,” offers Mike. “If I was working in a normal job as a machinist, it’d be doing the same thing all the time. For example, in one of the Australian Ballet shows we built recently we had to create a giant three metre high carved hand modelled on a Greek statue. It had to tip forward and allow the dancer to stand on the end of it, striking a pose. I’ve never built one before and I doubt I’ll ever build one again! No two things we build are the same.”
Each new show brings technical challenges that the workshop staff learn from. “Phantom of the Opera was a lot of automation and things we’d never built before, like floor traps, floor winches, and the system for the giant falling chandelier,” continues Mike. “Wicked had the big levitator system to make Elphaba fly, which itself was so large it was a challenge to integrate. Billy Elliot was physically challenging. The set featured a two-storey house and kitchenette with a small staircase which rotated while lowering completely into the floor. It had to go all the way into the basement, and contractors had to come in and dig a hole two and a half metres deep in the basement floor to fit it all in.”
In the vanguard of automation and construction for years, the workshop crew have seen a lot of advances in technology, as show designers keep trying to go bigger and better. “Designers often want you to create something that sometimes seems mechanically impossible,” Mike wryly observes. “Floors are always getting lower and lower to fit more automation in, and sets have to travel at faster and faster speeds. Sunset Boulevard had a 14 tonne mansion that drove downstage. In our current show, Moulin Rogue!, there’s a house set that weighs four tonnes that travels downstage and rotates. Quite often when you’re building shows that have come from other productions, information comes slowly and you don’t often have a lot of time for R&D. You just have to make it work. On Moulin Rogue! we’ve been using 3D printing and Computerised Numerical Control (CNC) routing for finishes and repetition work, and the show has an amazing look.”
With the theatre world in Australia firmly centred in Melbourne (sorry Sydney, but it’s true) why does Mike think that his workshop still gets the lion’s share of set builds? “It’s our staff, our managers, and the rapport we’ve developed with our clients,” posits Mike. “But it’s mainly the skill-sets of our staff and quality of the work they do. Once we’ve done good work for people, they keep coming back. Everyone says our scenery is unique in terms of quality. I’ve seen some builds from the US and the UK that I’d call substandard, but in the dark of the theatre and from out in the audience, they get away with it. But a set has got to put up with being taken apart, shipped, put back together, and still look the same. I like to think we’ve got the right people building the right sets. And we’ve been around so long, a lot of people from our workshop are now running shows in Sydney and Melbourne, so they have a strong connection to us.”
Does Mike have any concerns with TSA getting involved with the workshop? “Having TSA onboard is fantastic,” states Mike emphatically. “Stuart’s approach is brilliant, and he’s a switched-on guy. Getting us up to date with technology like CNC and TSA’s Raynok automation systems gives us the ability to do more. Collaborating with TSA on things like trussing, chain motors, and flying is good for both organisations. Our clients are excited.”

The New Blood Duncan Barton – Production Development Officer
With 20 year’s experience working on London’s West End for set builder TMS on shows like Phantom of the Opera, Les Miserables, The Lion King, and Mamma Mia!, Production Development Officer Duncan Barton relocated to Australia with his wife and three children three years ago. His first job with the scenery workshop was technical drawings for Billy Elliot, and he’s worked his way up from there.
“The Adelaide Festival Centre Scenery Workshop has an international reputation; in London I was aware of them as the biggest and best in Australia,” relays Duncan. “My day-to-day until recently was technical drawing and production management, but now with TSA at the helm, I’m doing more scheduling, meeting customers, bringing new work in, quoting, and then handing over projects to the workshop foreman. TSA are opening new people and markets to us. Previously, the theatre world knew of us, but that was about it. We are already talking to new people.”
While the workshop still does the same building and refurbishing of sets, and runs departments for carpentry, engineering, and sculpting, they now have a goal to create a new business infrastructure around them. “Industry in Australia isn’t really set up to support theatre,” explains Duncan. “We often have to bring in specialised equipment from the USA or UK, and we don’t like doing that. We want to start building up companies around us by feeding them work so we don’t even have to go interstate, let alone overseas.”
It’s not just supply that Duncan wants to diversify, it’s also their client base. “TSA allows us to go out and offer our services to more markets,” outlines Duncan. “The doors are now open, and we are finding work in schools, for architects, and with building firms, which wasn’t possible under the previous structure.”
Inside the Workshop
For the schools, the workshop can now offer set building and hire, rigging and automation via TSA, and maintenance programmes for school theatres. “Part of that is about educating schools about safety in their theatres, including issues like cloth fireproofing, and having regular safety checks for winches,” Duncan elaborates. “Architects can come to us for special projects and one-off pieces. For example, if a customer wants a sculpture or feature wall, we can do that. Last year, a school had a refurbishment and wanted a sculptured tree for their library. The architect contacted us, and we designed and built it. We’re the ‘arty’ side of architecture.”
There’s also more theatrical customers opening to the workshop. “We’ve built versions of Cabaret and Mamma Mia! for the University of Adelaide, and will be doing Urinetown for them as well,” says Duncan. “After these productions have been run, we can then hire the sets out to schools. We’re building relationships with schools and educating them about what goes into a theatrical production. We have schools come in for two-hour tours around the workshop, showing students what we do and how we do it. Theatre can be a black art to some people, and most of them don’t know what we do behind the scenes.”
With an updated one-stop-shop for production managers, the workshop is catching the eye of Film SA and the television industry. “We like mixing it up!” enthuses Duncan. “We’re looking at film and TV and it’s very interesting. Companies like Film SA are realising they don’t necessarily have to bring in crew from overseas or interstate. There are some TV projects that will keep our team excited and on the ball. I find if your crew are interested, they do quality work. Every day is different here, working with different materials and different people. It’s a unique place!”
Subscribe
Published monthly since 1991, our famous AV industry magazine is free for download or pay for print. Subscribers also receive CX News, our free weekly email with the latest industry news and jobs.