News
24 Jan 2018
Inside L-Acoustics: At a rural village in France
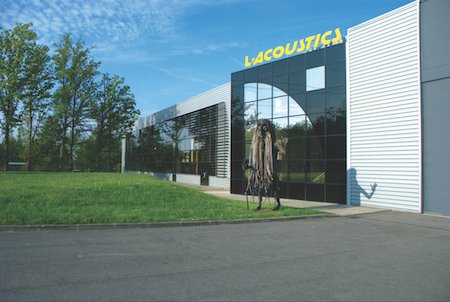
Subscribe to CX E-News
Inside L-Acoustics: At a rural village in France
By Julius Grafton.
When the company first located at the factory in Marcoussis, France, it was a rural site on a plateau above the village. Now it is a small industrial estate, dominated by four of the six factories that L-Acoustics occupy.
I visited HQ, which is the original factory. The factory floor was converted to research and development some years ago. More than 50 people work in that area alone. Strangely I was not invited inside. Several guys wheeled something about a metre tall out a door, it was covered in a black cloth. ‘That’s just the lunch’, my guide quipped.
This is LAC 1, guarded out front by an enormous steel statute creature with dreadlocks made from various cables. It is called Bob. Works of art are a feature at L-Acoustics, an expression of the culture of the founder and owner, Christian Heil. His surname is pronounced ‘Elle’, so the company which started as Heil Acoustics quickly became L-Acoustics – upon the suggestion of some from Germany.
Across the street is LAC 2, the factory, where about 50 people assemble speaker boxes. The cabinets come down from Northern France, where L-Acoustics own a company called Simea that builds and paints the boxes.
Down the road is LAC 3B which is the goods inwards store. It dispatches components to keep the factory 48 hours ahead. These components include the multi channel amplifier/ processors that drive all L-Acoustics products. These are built at what was the Camco factory in Germany, which is now fully owned by L-Acoustics.
Finished goods leave the factory and head for LAC 3C, the dispatch warehouse. The company has a good relationship with its workforce which, being French, is unionized. They work a 35 hour week, and after 10 days have one day off. They get 5 weeks holiday a year.
The factory is working at virtual capacity, with long term production planned a year in advance. This is refined each quarter. Currently they produce around 800 speaker boxes each week. They say they can step this up a little, and clearly have plans to step up even more since the new L-ISA system promises to boost demand.
Each speaker system is hand assembled from components that have been through quality assurance. A production line conveys each cabinet from one end to the other, and each line worker does a set of tasks for two hours and then moves to another station, to keep them fresh. In this way, assembly training can be implemented step by step. Down the end of the line, a robotic arm turns the cabinet as the packaging is applied. From start to finish, no one has lifted a speaker cabinet without mechanical assistance.
This article first appeared in the print edition of CX Magazine December 2017 as part of a special feature The live audio revolution pp.14-27 which included:
The Revolution has arrived: Spatial audio mixing – 3D Sound for the Stage
d&b Soundscape
Barco IOSONO
L-Acoustics L-ISA
L-Acoustics factory tour
d&b factory tour
CX Magazine is Australia and New Zealand’s only publication dedicated to entertainment technology news and issues. Read all editions for free or search our archive www.cxnetwork.com.au
© CX Media
Subscribe
Published monthly since 1991, our famous AV industry magazine is free for download or pay for print. Subscribers also receive CX News, our free weekly email with the latest industry news and jobs.